How Accurate Coating Thickness is Achieved with Your Powder Coating Machine
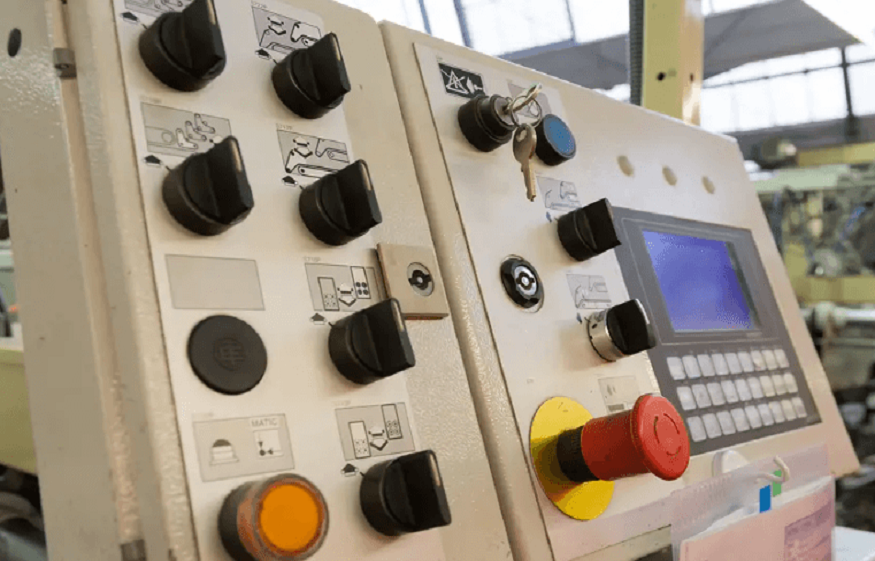
Every finish tells a story—especially in a workshop where details matter. Coating a surface isn’t just about color or shine; it’s about precision. That smooth, even finish depends on how the powder coating machine is set up, maintained, and understood by the operator.
Voltage Stability Enhances Uniform Powder Deposition
Voltage control doesn’t just power the process—it shapes it. Inside a powder coating machine, consistent voltage helps ensure powder particles are drawn evenly across the surface. If the charge fluctuates, so does the finish. Low voltage can cause uneven spots, while surges might overbuild powder in certain areas. A stable voltage output helps the particles cling uniformly, reducing patchiness and delivering a clean, professional look.
Operators who work with steady voltage notice fewer touch-ups and better first-pass transfer efficiency. It’s not just about having a good power supply; it’s about regulating that power carefully through the machine’s control system. A fine-tuned setup makes a big difference in how the final layer settles, especially on parts with grooves or edges.
Particle Size Control Dictates Consistent Layer Depth
Powder might look like dust, but it behaves more like a liquid once airborne. The size of each particle influences how it moves, sticks, and builds up. Smaller particles may coat thinly but more uniformly, while larger ones could lead to heavier, uneven build-up. By managing the size distribution of powder in the hopper, a coating technician can predict and control layer thickness more accurately.
Inside a powder coating machine, proper fluidization of the powder feed and use of sieves or filters ensures a consistent blend. Without this control, parts might end up with areas that are either undercoated or too thick, which can cause peeling or surface flaws during curing. That’s why modern machines rely on finely tuned delivery systems and tight control over powder characteristics.
Digital Mil Gauge Validation Confirms Coating Accuracy
Guesswork doesn’t belong in a finishing booth. That’s where digital mil gauges come in. These handheld tools measure dry film thickness quickly and accurately, confirming whether the powder coating machine is applying material as expected. Technicians use them before and after curing to compare the projected and actual thickness.
What surprises some is how often these gauges reveal inconsistencies that can be fixed with minor adjustments. Whether it’s tweaking gun distance, adjusting powder flow, or checking voltage again, the gauge keeps quality in check. It takes the mystery out of coating and replaces it with numbers you can trust.
Electrostatic Wraparound Reduces Thickness Variability
Flat panels are simple. It’s the curves, corners, and odd-shaped parts that really test a machine’s performance. A well-calibrated powder coating machine creates an electrostatic field that helps powder particles “wrap” around these surfaces. That wraparound effect ensures full coverage—even in the spots that don’t face the gun directly.
It also prevents one side from getting more powder than the other. Without wraparound, parts can come out with light areas that don’t pass inspection or thick blobs that won’t cure correctly. In powder coating, even distribution isn’t just about what you see—it’s about what gets hidden. Electrostatic balance makes sure all those hidden spots are treated equally.
Spray Pattern Customization Secures Even Application
No two projects need the same spray pattern. A flat panel might require a wide, gentle fan, while a narrow rail needs focused precision. The powder coating machine’s gun must be adjustable to match these needs. An operator can shape the pattern to control how powder lands and spreads, preventing buildup on edges or missed areas.
Changing the pattern isn’t guesswork—it’s guided by part size, geometry, and coating goals. Smart adjustments reduce overspray and improve finish quality. In high-production environments, where each part must meet exact specs, that ability to fine-tune patterns becomes more than a convenience—it’s essential for accuracy.
Consistent Air Pressure Regulates Powder Flow Accuracy
Air pressure inside the powder coating machine plays a silent but powerful role. It pushes powder from the hopper, through the gun, and toward the part. If the pressure drops, powder dribbles. If it spikes, powder blasts out unevenly. In both cases, the finish suffers.
Maintaining consistent pressure means fewer surprises. Operators usually dial in both the atomizing and conveying pressures to maintain a steady flow. With the right setup, powder flows like a well-mixed paint stream—smooth, predictable, and controllable. That control means more accurate coating thickness and less wasted material.
Controlled Powder Delivery Sustains Coating Uniformity
A reliable powder coating machine delivers powder in a steady, predictable way. From hopper agitation to feed pump design, every component plays a role in how the material moves. Interruptions or inconsistencies in delivery can create ripples in the finish—thin spots, uneven coverage, or texture shifts after curing.
Good machines allow operators to adjust feed rates based on part complexity and powder type. Once the delivery system is locked in, the finish stays consistent across batches. This consistency is why experienced coaters trust high-quality equipment—it doesn’t just put powder on metal; it does it with the kind of precision that makes customers come back.